宇航裝置中的冷凝器按照儀表和特殊要求安裝在倉室的內外表面,這些部位必須承受規定的溫度規范。因此,由這些壁板結構重復建成圓柱體型內外部薄殼體并形成溫度調節系統的裝置。冷凝器壁板結構上提出2層無縫連接,在長度上相鄰兩部分之間要有溝槽,以便熱介質循環(圖1a)。
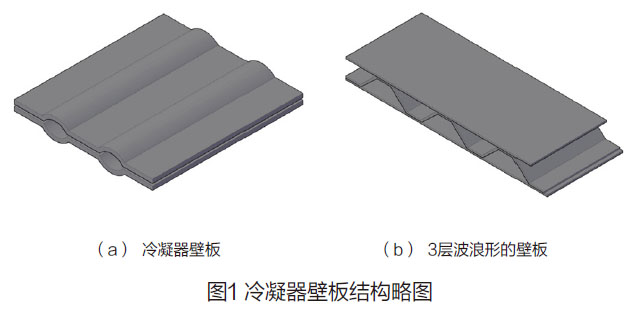
溝槽截面具有規定幾何形狀,一個溝槽本身可以具有一個或兩個面。使用材料為鈦合金TC3,冷卻片的厚度為1~1.5mm。
制造壁板傳統工藝過程包括兩層板在軋制中連接,由于軋制連接不能保證在焊接條件下的溝槽幾何尺寸 ,造成在隨后工序中報廢率高達到70%~80%。
在某些裝置中,冷凝器的功能被制成3層波浪形壁板(圖1b)。這里,用于溫度調節介質的通常為液態氮。此外,這樣的結構也用于主整流罩的外殼。模具結構是波浪形圓柱體或錐體,用鉚釘與殼體內部平滑連接,用氬弧焊與殼體外部連接。焊縫的極限密封水平限制在零件的使用期限內。鉗工的鉚接工作量很大。
況且現有技術采用熔化焊接,毋容置疑,在焊縫處,嚴重損害了材料的力學性能,尤其是沖擊韌性降低明顯;且沿著焊縫留下了應力腐蝕源,從而降低了抗應力腐蝕壽命。該方法所制波浪形溝槽尺寸精度難以控制。
一、2層壁板新的制造工藝
提出的工藝方案,歸結到隨后在一個工位上緊密閉合模具并在氬氣環境下使得氣體供給轉到毛坯溝槽成形處,在900~930℃以及1~1.5MPa的氬氣氣體壓力下成形20~30min;在兩層板間氣體壓力作用下,進行擴散焊接工序。
因此,溝槽分布精度及其幾何形狀由模具精度來確定,精度得以大幅度提高,并且在固相中的擴散焊接沒有破壞材料的組織,達到與母體材料等強度,以保證高水平腐蝕壽命及幾何形狀。
表1給出加工步驟和規范。
整個鈦合金壁板成形工藝過程包括:施以防擴散涂層(氮化鈦),將鈦含量約80%的氮化鈦,在500℃真空爐內施涂于對應板坯溝槽表面;在氬氣中焊接或在必需的溫度中加熱一段時間,在氣體壓力下的真空中焊接。
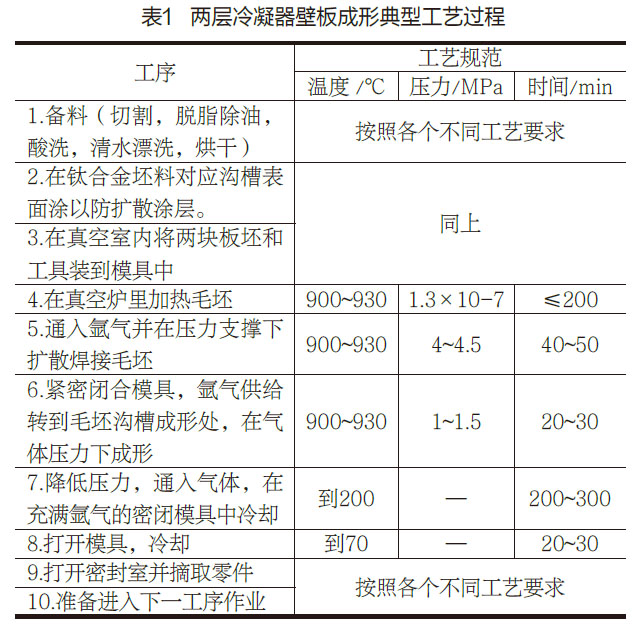
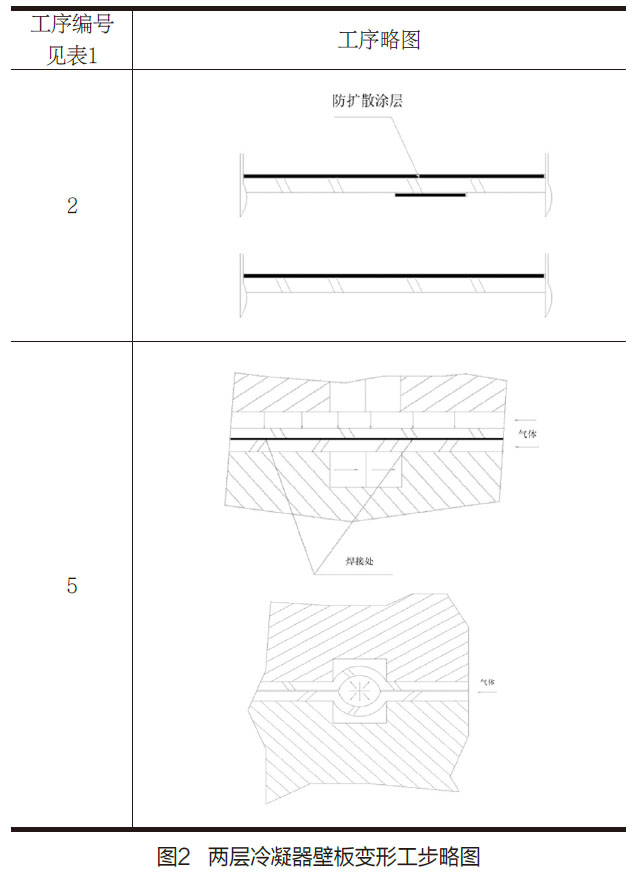
應當指出,在固相中的擴散焊接沒有破壞材料的組織,達到等強度,以保證高水平腐蝕壽命及幾何形狀。
二、3層冷凝器壁板新的制造工藝
設計了波浪形壁板新的結構并擬定了新的工藝。緊密閉合模具并在氬氣環境下使得氣體供給轉到毛坯溝槽成形處,即在875~930℃以及1~1.5MPa的氣體壓力下拉深成形20min,保壓10~15min。工藝過程還包括板疊中板材的氣體擴散焊接。工序排列和規范列于表2,主要工序略圖見圖3。
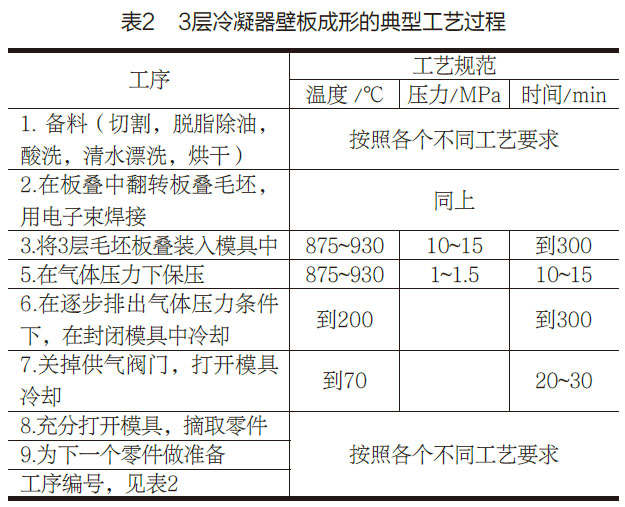
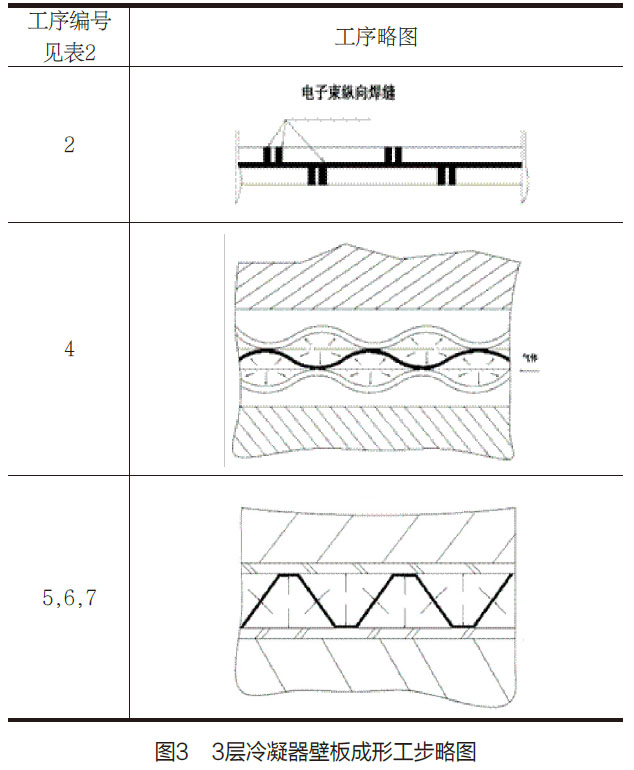
制造冷凝器壁板和波浪形壁板共同工序包括:連接和成形。在第一種情況下,用擴散焊接連接板疊;在第二種情況下,用熔化焊接。與用氣體成形工藝作用效果是一樣的。冷凝器的兩層壁板和3層壁板工業實樣分別示于圖4和圖5,使用板厚1mm;在設計的高度10~30mm時,結構的外廓尺寸達到500×500mm。
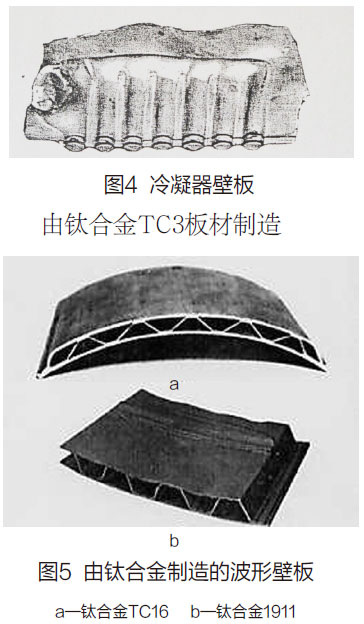
三、結論
與傳統的制造方法相比較,由于采用新的結構和工藝,零件連接部位的強度增加30~50%;零件的材料消耗減少20~30%;由于去除了熔化焊接和鉚接工序,連接處的精度提高
2~4倍;零件數量減少到1/5~1/10;由于同樣的制造工序制造勞動量減少了1/2~2/3,并且減少了裝配和精加工工作量。
相關鏈接